'Stacks on the mill’ a winner for The Terrace
Media Release
October 31, 2013
‘Stacks on the mill’ a winner for The Terrace
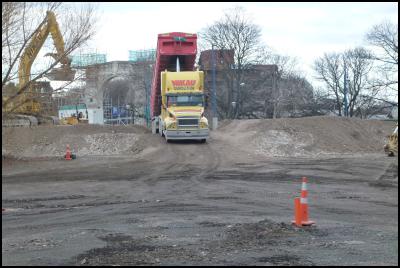
Click for big version.
(The Terrace land preparation JPG):
Demolition rubble is trucked on to The Terrace site and stacked up to four metres high.As foundation work begins on the new entertainment and office complex The Terrace, in Christchurch, simple Kiwi engineering common sense from Aurecon has meant significant savings in time and money, and reassurance for the developer that the complex is going to be safe.
Geotechnical assessments of the site, on the banks of Christchurch’s Avon River, showed that layers of sand and silty sand approximately 20 metres below ground level were potentially liquefiable in a strong earthquake. While close to the surface, a compressible soil layer - which is the remnant of an old stream bed - had potential to allow foundation settlement under the weight of the building.
How to make the ground stiffer, was the challenge that faced Aurecon. The company’s Technical Director, Stephen Hogg, says it was known from the outset that staying out of the water table was necessary in order to save time and money.
For the owner of the property, Antony Gough, the solution also had to ensure the safety of the building, which he describes as “paramount”.
He
says prior to Aurecon’s solution, four options had been
considered and rejected:
• Deep piles down
25 metres, which was rejected due to the potential for
future earthquake movement to cause soil lurch (or ground
displacements) which could effect the structural integrity
of the building
• Digging out the surface
soil and replacing with hard fill imported from local
quarries. The extent of dig out was not precisely known and
would have involved about 900 truck movements on local
roads
• Remaking the ground to a depth of
about three metres by adding cement to the site soils. This
is a viable option being used elsewhere in the Christchurch
CBD but this particular site is three metres above the water
table and major dewatering was likely if soil was removed
down to the three-metre level. It was rejected because of
cost.
• Rammed gravel columns, which
penetrate the surface soils down to the upper gravel layer.
This option was rejected because of cost.
“This is
where Aurecon stepped in. They came up with an extremely
effective solution similar to the old game of ‘stacks on
the mill’.”
Aurecon’s Stephen Hogg says the site
was overloaded with heaped demolition rubble to apply weight
heavier than what the new buildings will be.
The fill was trucked on to the site from a few hundred metres away and stacked four metres high and left for about four weeks. About 5000m3 of fill was moved (800 truck loads) with a total weight of about 9000 tonnes. The total weight of the building will be about 6000 tonnes.
Surveyors, using precise optical equipment, frequently measured the effect of the heaped demolition rubble on the site. These measurements continued until the settlement effect caused by the stockpiles ceased, at which time the rubble was removed from the site.
“The impact on the roading system and traffic flows was lessened and it was cost effective, good for the environment and good for the economy,” Mr Gough says.
Mr Hogg says the preloading treatment has meant that the buildings do not need complex or deep-seated foundations, as would have been the case. Aurecon also designed a reinforced concrete raft foundation that will allow the buildings to float on top of the pre-compacted soil, which will minimise the effects of differential settlement if deep liquefaction occurs in any future earthquake.
“We gained a month because the raft foundations did not have to be fully designed before pre-loading the site. The design was completed while we waited for the ground to settle. “
The concrete raft will mean the building will float on the upper levels of the ground, providing a robust foundation structure that will be strong and tolerant to settlement.
“It will also distribute the effects of potential differential settlement rather than concentrate the damaging effects, as would be the case with a piled solution or pad foundation solution.
“It will also mean we can easily re-level the building in the future should it be necessary.”
Mr Gough says the fact that work is already under way “is testimony to Aurecon’s smart thinking”.
THE TERRACE FACTS
•
Stage 1 will appear as three buildings on Oxford
Tce and one on Hereford St. It will be hospitality on the
ground and all of the first floor areas in the Oxford Tce
buildings. It will include office space on the upper levels
in these buildings.
• Stage 2 will be the
major large office building on the corner of Cashel and
Oxford Tce that will contain approximately 6000m2 of office
space and retail plus hospitality on the ground floor. It is
due for completion in early 2016.
• Stage
3 will complete the Cashel St frontages and is likely to
contain retail on the ground floor and a 100 bedroom hotel
above.
• Stage 4 will be the final stage
and it is expected to contain a 320 bay car park sleeved
with apartments to sell on both its north face facing
Hereford St and the west face facing the central piazza and
the Avon
River.
ENDS